SAND AND SAND MINING
Part I
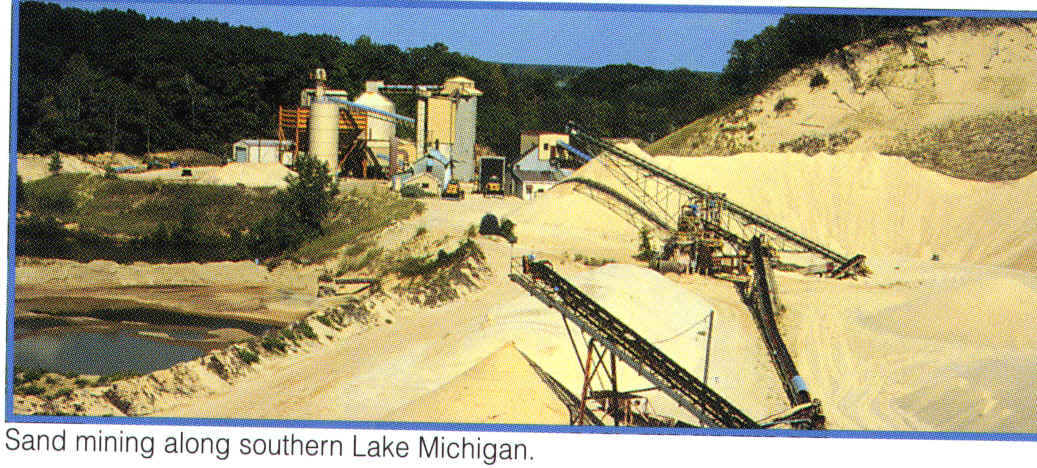
Source: Unknown
Uses of sand
This resource is sand, not sand and gravel. Its primary source
is sand dunes, therefore Michigan ranks third in the US in industrial sand production.
Silica sand is the major component of glass, foundry molds, and abrasives. It is also used
in ceramics, on golf courses, and as a filter medium. In the midwest, the major uses of
the sand are in the foundry and automotive industry operations.
Dune sand has a number of uses. The size, uniformity, chemical purity and
nature of dune sand make it a singular resource. The demand for this resource is
increasing, because of an increase in the number of products using dune sand and because
other new uses have been developed.
SAND USED IN FOUNDRIES
The major use of dune sand is in foundries. The sand
is used to make molds and cores. The molds are used to form metal into a variety of
shapes. Core sand fills the spaces where metal is not needed or wanted. The requirements
are very demanding. Dune sand is particularly suited to foundry use because 1) it can
withstand the high temperatures (from 1,300� to 1,700�C) of the molten metal, 2) it can
withstand associated pressure, 3) gasses can escape through the sand, and 4) the sand has
the proper texture and composition to make a smooth casting and does not react with the
metal. Sand properties are checked regularly in most foundries. At best, the sand can be
recycled only about twice before it can no longer be used and becomes a waste product.
With treatment, these sands can be used as landfill. Most of the
industrial sand (molding, core, and glass sand) is obtained from the sand dunes along the
east shore of Lake Michigan.
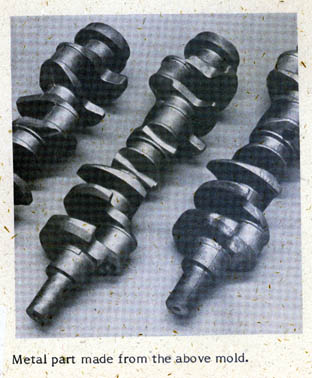
Source: Unknown
Sand casting and glass making are two of the oldest industrial processes known. There is
hardly a manufactured product made or an industrial process used that does not utilize
some form of these two industrial techniques in its makeup or in its fabrication. The
fixtures and tools used to make almost all manufactured products are made from sand
castings. The tools to make these tools were made from sand castings and so on ad
infinitum. Therefore, any decision affecting the cost and availability of industrial
sand will have a wide reaching, multiple effect on the cost and availability of almost
every manufactured product and its competitive advantage in the market place. The elevated
financial position of the foundry industry attests to the economic importance of
industrial sand and its total impact on all other industries, and ultimately the cost of
almost all fabricated goods sold.
Industrial sand is one of the more select types of sand found in
Michigan. This type of sand is needed because of its high chemical purity, grain size,
shape, and distribution. Sand and sandstone meeting these specifications are used in metal
casting and glassmaking. Some sand is also used as a scouring agent, traction sand in rail
transportation, lining for high-temperature furnaces, and in the manufacture of
metallurgical alloys. Thus, one aspect of sand and gravel mining that is not often
realized is that many sites are simply sand mines. Often we think of a sand
and gravel operation as one where both are mined at the same time, and through
sieving they are separated and sold as discrete products. However, in dune areas
clean, pure sand alone is mined and utilized.
Glass and molding sand production of the leading producing states in 1973
Sand for glass |
Sand for molding and
casting |
|
Thousands of tons |
Value
(thousands of $) |
Thousands of tons |
Value (thousands of $) |
California |
1,421,000 |
7,154,000 |
W |
W |
Illinois |
904,000 |
2,450,000 |
710,000 |
2,537,000 |
Michigan |
535,000 |
2,018,000 |
4,466,000 |
10,402,000 |
New Jersey |
2,118,000 |
9,798,000 |
808,000 |
3,900,000 |
Other |
5,593,000 |
21,724,000 |
3,039,000 |
11,702,000 |
Total |
10,571,000 |
43,144,000 |
9,023,000 |
28,541,000 |
Early foundries removed natural sand from small pockets along river banks
and local sand hills as their needs dictated. These sands were a composite mixture of
sand, clay, and other materials. Since the early 1900's, industry demands and its
associated advancing technology created the need for unbonded sand. Unbonded sand has very
little clay or other impurities present. Dune and coastal strip sands and crushed
sandstone are the leading sources of unbonded sand. The industrial advantages of unbonded
sand are: (1) more uniform grain size, (2) greater tolerance to heat, (3) less bonding
material and moisture required (additives) , (4) workability, and (5) greater suitability
for a variety of foundry uses.
One of the prime indicators of superior sand quality is fineness of
grain size. Grain fineness is a measure of the amount of sand passing through certain
screens. Grain size and shape affect both the escape of hot gases from the molten metal
poured into the mold and surface texture of the casting. The finer the sand used the
smoother the finish. Generally speaking, finer grained sands are used on smaller size
castings. Extraneous material, such as clay or broken sand grains, will plug off the pore
spaces of the mold causing blistering, pock marks, and weaken the casting. The sand grains
themselves must be durable so that the sand may be reclaimed and reused time after time
up to 25 times or more depending on the type of casting and technique
employed.
The chemical quality of the sand is also important. The sand must
contain less than 2% carbonate. If too much carbonate is present it reacts with acid based
binding material and causes the prepared mold to lose strength. Other extraneous minerals
such as mica and feldspar cause the mold to react with the molten metal causing abrasions
and weakening of the cast.
SAND USED FOR GLASS MANUFACTURING
Silica (quartz) sand is also used in glass manufacture. Quartz comprises 50-65% of
the mix used to make glass. The high purity of dune sand makes it especially useful in
some glass manufacturing. The quality of sand used for glassmaking is highly
restrictive. Specifications for glass sands generally require a specific range of grain
sizes which produce even melting. Chemically, the sands must be over 98% pure silica and
contain practically no impurities, especially metallic oxides. As little as 0.001%
metallic oxides will impart color to glass. Other included minerals with high melting
temperatures, such as garnet, will cause "stones" or spots to appear in the
finished glass. Most glass companies prefer to have nearly pure silica sand (99.5% or
greater purity) to which they will add their own desired special ingredients. This is
particularly true in the case of optical glass, which has very high silica and very low
metal oxide content. Some fiberglass and amber colored glass bottles are made from
processed sand from Bridgman and Muskegon.
OTHER SAND USES
Railroads use large amounts of sand to improve traction on wet or
slippery rails. Sand is used in sandblasting. The floors of some large open hearth
furnaces are line with silica sand. Sand is an excellent filter for removing sediment and
bacteria from water.
One area of increased use of sand is in fiberglass manufacturing.
Fiberglass is used to reinforce many plastic products. These products are enjoying
increased use in processes where lightweight corrosion-resistant materials are desirable.
Boats, cars and airplanes are some of the products finding increased uses for fiberglass.
The petroleum industry also uses sand. Under pressure, sand is injected
into an oil well. The sand goes into the cracks and crevices where the oil is trapped.
When the pressure is released, the sand helps hold the cracks open. When this process
works, oil production can be increased greatly. The process is called sand-fracturing.
Stockpiled sand, whether delivered by conveyor, truck or pipeline,
requires some processing. At a minimum, washing and drying the sand is necessary. If the
sand is to be transported by Great Lakes vessel, the washing and drying process is usually
done at the destination terminal. For sands that are unusually high in iron or calcium
carbonates, beneficiation is necessary. This process utilizes magnetic and float
separation to remove impurities. After the sand has been washed and dried and contaminants
have been removed, it is screened. In this process, sand is separated according to grain
size and stockpiled for future blending.
These numerous demands for sand require mining of our dunes and other
sand resources. Michigan is one of the largest producers of dune sand in the United
States. Demand appears to be increasing. Yet, the supply is nonrenewable and decreasing.
Sand mining in Michigan is concentrated along the Lake Michigan
shoreline with some mining taking place at inland locations. All the sand dune operations
except one (Mackinac County) are in the Lower Peninsula, from Mason County to the Indiana
border. These operations are now monitored under the Sand Dune Protection and Management
Act. This legislation is intended to protect the environmental value of the dunes from
uncontrolled sand mining.
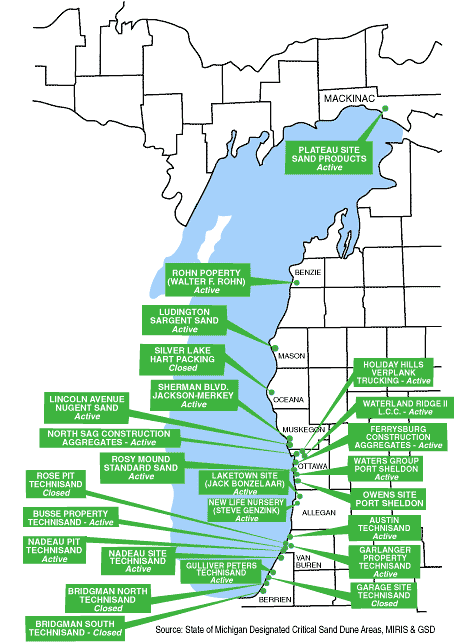
SAND DUNE MINING OPERATIONS ON LAKE MICHIGAN, AS OF 2000
Michigan has the largest number of fresh water sand
dunes in the world, but mining has put the Michigan landmarks in danger of vanishing.
The dunes were created during the last ice age and have grown for thousands of years. Once
destroyed, as in the mine below, the dunes cannot be replaced.
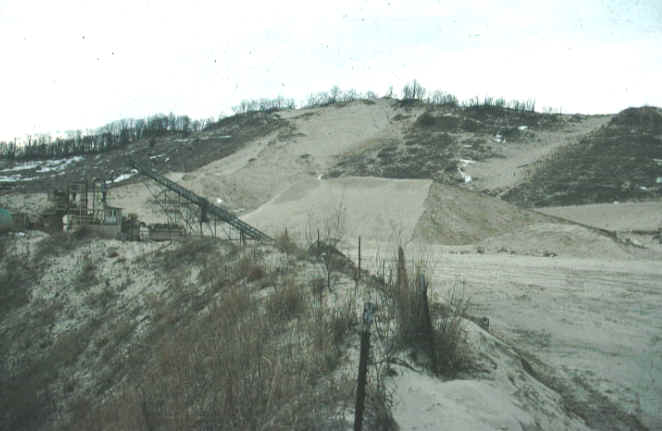
Source:
Photograph by Randy Schaetzl, Professor of Geography - Michigan State University
SAND RESOURCE TYPES AND THEIR LOCATION
In Michigan, there are three important dune areas where industrial sand is mined. These
are 1) inland dunes, 2) coastal
dunes, and 3) coastal sand strips. A mineral resource with similar characteristics to
dune sand is sandstone; the Paleozoic Sylvania sandstone is mined in only one very limited
area of the state.
Inland dunes are sometimes located up to 30
miles or more from the present day Great Lakes shore. These are older dunes that were
formed by wind action some 4000-8,000 years ago. Inland dunes usually exist in the form of
ridges, small hills, and knolls found on ancestral lake beds and outwash plains. The best
developed inland dunes may be 30 to 40 feet in height and are found predominantly in the
eastern UP and the Saginaw Bay area. Inland dune sand usually has a slightly higher silt
and clay content, smaller, more angular grains, and a slightly differing chemical
composition than coastal dune sand. In addition, being much older and not subject to as
much wind and wave action as the coastal variety, these sand features are usually well
stabilized with protective vegetative cover.
Coastal dunes are found predominantly
along the eastern shoreline of Lake Michigan from the Indiana state line to the Straits of
Mackinac. Additional dunes are found along the Great Lakes shoreline in eastern Saint
Clair, Alger, Luce, and Houghton Counties. Coastal dune sand is generally free of silt and
clay, has a common range of grain sizes, and is generally more rounded than other types of
sand deposits. Coastal dunes usually reach a height of over 100 feet above the surrounding
terrain and form prominent knolls, peaks, mounds, and ridges. When not stabilized by
vegetation, they are extremely unstable and migrate in the direction of the prevailing
winds. Good examples of coastal dunes may be found at Silver Lake State Park in Oceana
County, Warren Dunes State Park in Berrien County, and in the Sleeping Bear National
Lakeshore in Benzie and Leelanau Counties.
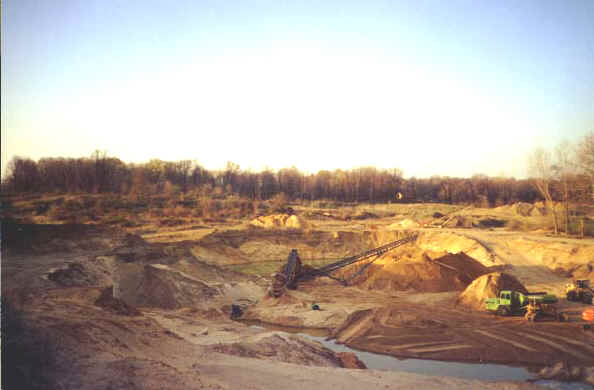
Source:
Photograph by Randy Schaetzl, Professor of Geography - Michigan State University
Coastal sand strips can be found along all of Michigans Great
Lakes shoreline. They frequently occur with very low, wind-formed ridges near present
shorelines. Coastal sands are generally free of clay and silt and physically resemble
sands found in the dunes. However, the sand usually has a higher proportion of carbonates,
such as limestone and dolomite. Some people consider coastal sand strips to be the
beginning stages of dune development.
The only sandstone presently used for industrial sand purposes
the Sylvania sandstone crop out in southeastern Wayne
County. This unique white sandstone consists of small grains of silica, smaller than those
of dune sand. Very few impurities are present. This sandstone deposits is important since
Sylvania sand is used principally by the glass industry in making a variety of special
glass products.
The Sylvania Sandstone
Devonian rocks supply a variety of mineral resources. A Devonian sandstone formation known
as the Sylvania Sandstone located at or near the surface in Wayne and Monroe counties
contains high silica, uncontaminated sand grains. Mining sandstone involves different
techniques (i.e., blasting, crushing, etc.) and the process is more expensive. However,
the requirements of the glassmaking industry for high-silica sand with negligible
contaminants motivate the operators to mine the sandstone, even at great expense.
From the outcrop of the basal Sylvania sandstone in Wayne and Monroe counties we obtain
sand used in the manufacture of glass. Some of this sand is so free from iron, the most
vexing impurity, that the sand is suitable for optical glass.
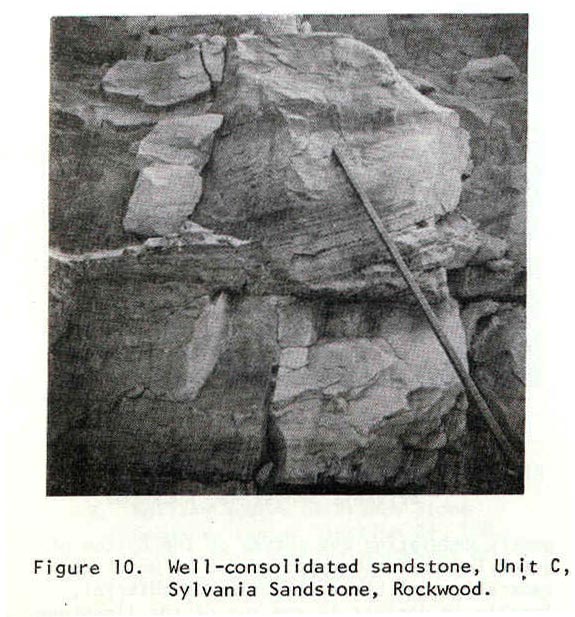
Source: Unknown
During and shortly after World War I most of the glass used for the
manufacture of optical glass for the federal government was obtained from the Michigan
quarries. The sand is now used for the manufacture of plate glass, fine table glassware,
and common glassware of many uses. These sandstone beds are believed to be ancient dunes
blown up on the shore of an ancient Devonian sea. As we trace the Sylvania towards the
center of the Michigan Basin, we find from the logs (records)
of wells drilled into it that it becomes thicker with lenses of limestone and shale, and
that the porous parts of the formation contain brines. These brines are in use as brine
reserves for chemical industries, and also possible oil and gas
reserves.
The map below shows where active sand mining operations exist. Other areas where
sand is mined include inland sand areas (usually glacial outwash), and sandstone areas
(Detroit).
Many sand dunes are protected under the Sand Dune Protection
and Management (SDP&M) Act. Mining the dunes has the distinct advantage of being able
to transport the sand by freighter, and the industrial markets that are linked to the
water routes of the Great Lakes are many. A substantial amount of dune sand is shipped
from Ludington, Mackinac, Muskegon and Ferrysburg. Of Michigans 3288 miles of Great
lakes shoreline, only 270 miles is protected under the SDP&M Act. Use of industrial
sand is declining in the US in large part because of recycling at the factories. Mining
sand dunes is a highly controversial topic, since Michigan values its dunes so much.
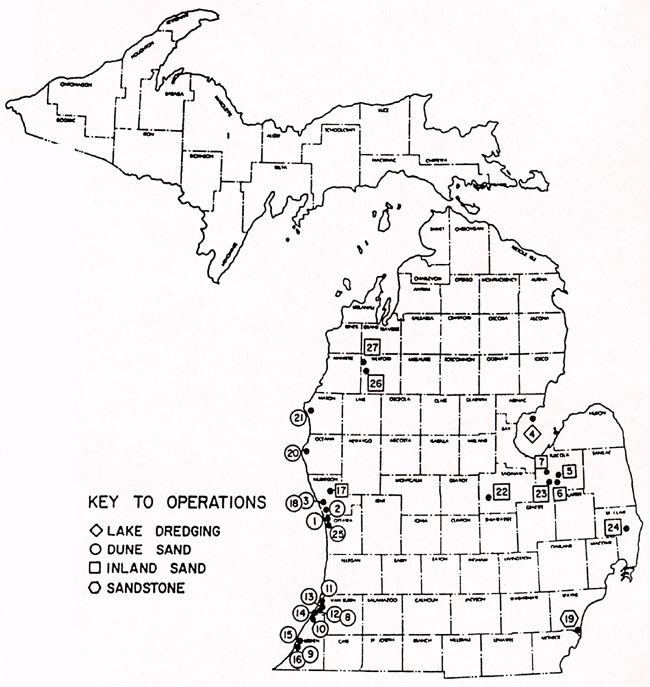
Source: Unknown
If we restrict the map to showing only DUNE-mining areas, note (below) how the
distribution changes.
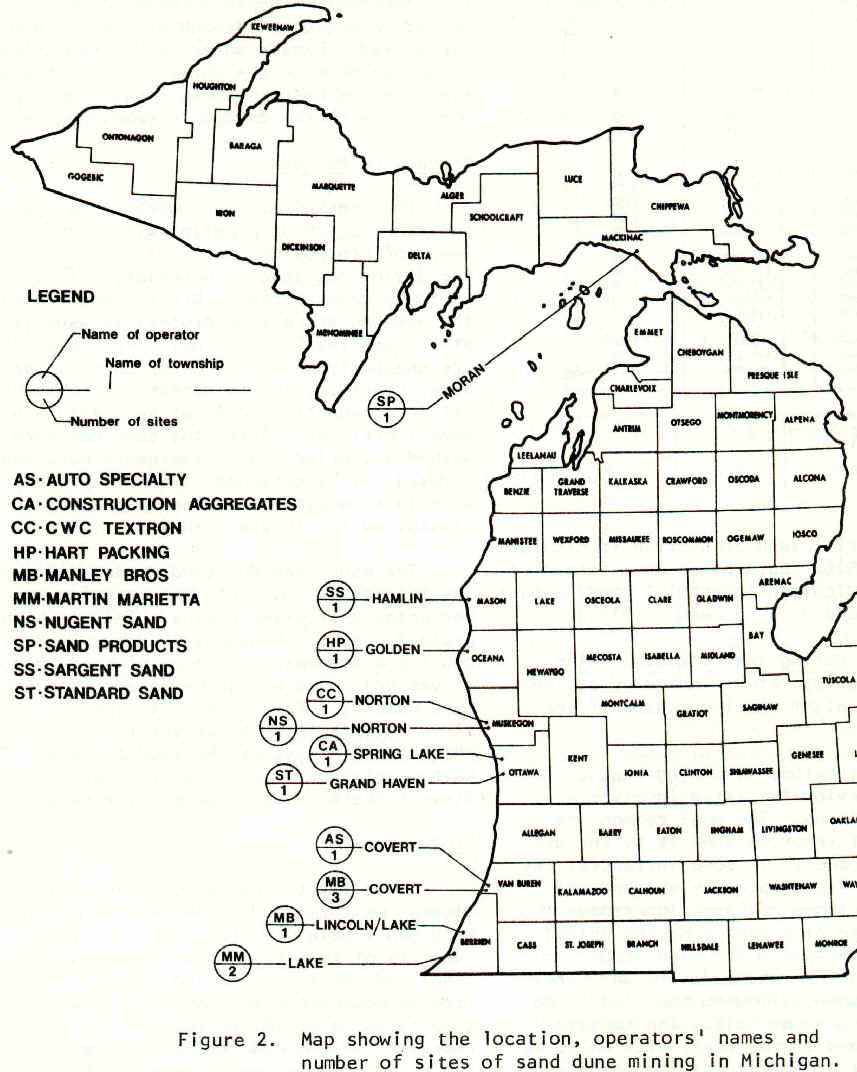
Source: Unknown
For a shortcut to Part II, click here.
Much of the text and imagery on this page is from a 1975 Michigan Geological
Survey Division Circular (#11), by J. Lewis.
This material has been compiled for educational use only,
and may not be reproduced without permission. One copy may be printed for
personal use. Please contact Randall Schaetzl (soils@msu.edu)
for more information or permissions.
|