SAND AND SAND MINING
Part II
SAND MINING ECONOMICS
Both mineral and sand mining industries have been on the Michigan scene for over a
century. Table 1 provides a further breakdown of the production and value of sand for
industrial uses.
Table 1 - Production and use of industrial sand in Michigan in 1973
Uses of the sand |
Production (tons) |
Value ($) |
Molding |
4,466,000 |
10,402,000 |
Glass |
535,000 |
2,018,000 |
Traction |
295,000 |
710,000 |
Other (scouring powder, furnace sand, and
hydrofacing sand) |
433,000 |
1,087,000 |
Total |
5,729,000 |
14,217,000 |
Historically and economically, those industries concerned with specific
mineral utilization are located near a minable source of supply of that mineral. The
foundry industry, which is dependent upon several mineral commodities, originally followed
the coal or lumbering industry for its energy needs. Another consideration for bulk
mineral users was proximity to cheap water transportation. Raw materials not found at the
site could be imported by water at a better competitive price while at the same time a
more economical way to ship bulky finished products was at hand. Limestone and clay for
foundry use were often secured locally and brought in by truck or railroad.
As the foundry industry evolved over time, its associated technology
placed more stringent requirements on the quality of sand used in its metal casting
processes. Early foundry sands often were imported from southeastern Ohio. During the late
1910's and early 1920's, larger and larger quantities of dune sand began to be used in
Michigans foundry industry as machines replaced manual labor and industrial
expansion continued apace. New metal casting processes required a higher quality sand. At
this time, it was found that some Michigan sands could not only withstand the extreme
temperatures needed for pouring molten steel but were also more durable, cheaper to mine,
and required little or no treatment prior to use in the casting process. Sand with these
same characteristics is also preferred by the glassmaking and other minor sand dependent
enterprises.
MINING, PROCESSING, AND RECLAMATION
Surface mining is the most common method of sand extraction. In this process, a front-end
loader (see below) or crane with a clam shell (also below) is used to move sand . Sand is
removed from the dune and loaded directly into a hopper where it is rough screened. After
screening it is either loaded into trucks or onto conveyor belts and transported to a
storage stockpile.
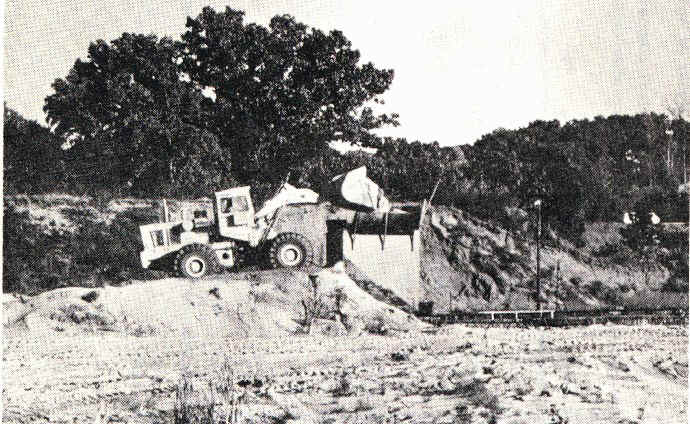
Source: J Lewis,
Michigan
Geological Survey Division Circular (#11), 1975
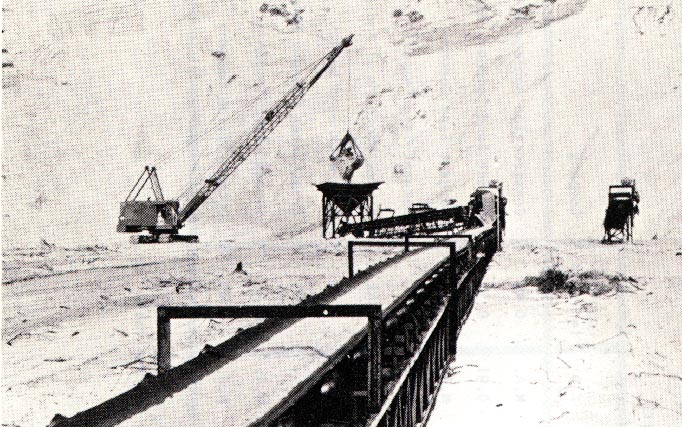
Source: J Lewis,
Michigan
Geological Survey Division Circular (#11), 1975
The dredging method of sand mining (see below) is somewhat more costly
and requires more elaborate equipment. The principle of this operation is to jet water
under high pressure against the dune bank or pond bottom making a sand slurry. This slurry
of riled sand is then sucked up by another pipeline and transported to a surge tank or
storage pile. The water transporting the sand is recovered and returned to the pond. A
dredge can mine sand to a depth of 20 m below the water surface.
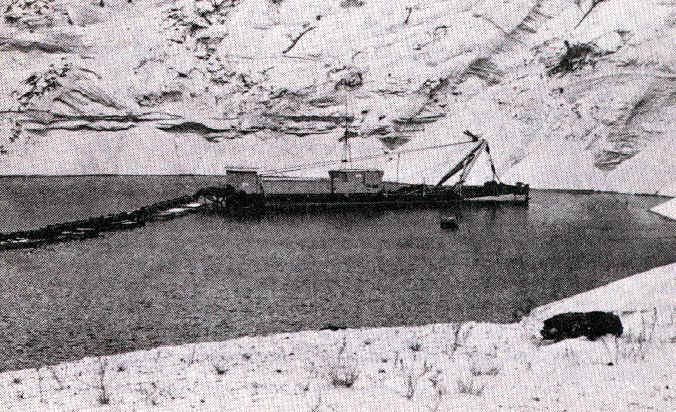
Source: J Lewis,
Michigan
Geological Survey Division Circular (#11), 1975
Hydraulic mining is very similar to dredging except the operation is
conducted from a portable stand rather than from a dredge. Water is ejected under several
hundred pounds pressure from a swivel nozzle which is mounted on the stand. The
pressurized water stream is aimed at a dune bank, washing it down into a small holding
pond (see below). From this point, the sand is pumped through a pipeline to a surge pile.
Once the sand slurry reaches the surge pile, the water is drained off and recycled back
through the high-pressure water line to be used again.
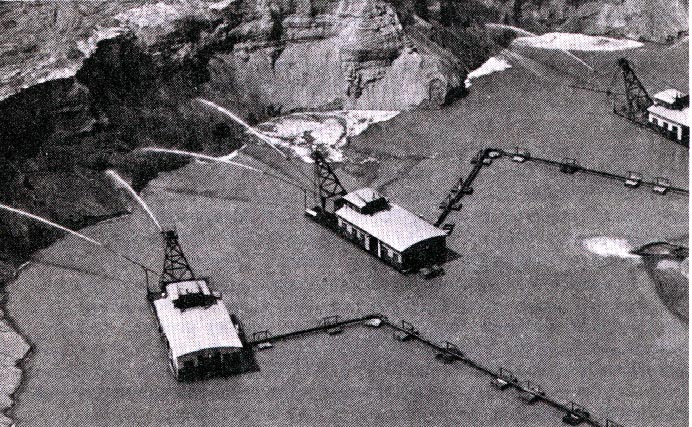
Source: J Lewis,
Michigan
Geological Survey Division Circular (#11), 1975
Unlike sand, loosely cemented sandstone usually requires drilling and
blasting before it can be mined. After overlying soil and unwanted rock have been removed
holes are drilled and explosive charges are placed in them and detonated. The rock is
broken into pieces that are small enough to be handled by front-end loaders. These pieces
are loaded into trucks and transported to the plant for crushing and screening.
NEEDS OF THE SAND MINING INDUSTRY
Industrial quality sand must meet certain prescribed chemical and physical properties,
must be located near its market, and must be mined, processed and shipped economically.
From the industrial viewpoint, location of proven sand
resources relatively near to market or to transportation facilities is second in
importance only to the quality of the sand deposit. Because the sand must be transported
to the market, transportation costs are an important economic factor. The heavy (sand)
product needs to be transported at minimal cost. Long distance hauling cost is minimized
by ship and rail transportation. Shorter haulage is usually provided by truck and is,
hence, more expensive. In many cases, transportation charges are several times more costly
than the value of the sand itself.
In addition to location, sand must be available
in sufficient quantities to assure its long-term availability to the industry.
Availability of the resource must also be coupled with reasonable access to the resource
itself. Public or private land ownership and local regulations, for example, all affect
the industrys capability of mining sand resources.
Mining costs are another important
consideration of the industry. The more expensive the extraction process the greater the
cost that must be passed on to the consumer of the final product. Included in the cost of
mining are blasting, removal of overlying rock and soil (overburden), mechanization, and
reclamation of the mined area.
The last major consideration of the sand mining industry is ore processing costs. Processing costs, like mining costs, must be
kept as low as possible. The final product industrial sand must be nearly
free from deleterious or undesirable minerals. Added treatment costs to remove unwanted
material such as roots and rocks, increases the market price accordingly. Both the foundry
and glassmaking industries must adhere to stringent physical and chemical sand
specifications. Changes in processing techniques utilizing less desirable types of sand
would require changes in technology with an attendant increase in cost.
In terms of the industrys economic impact, a 1975 newspaper
article stated that there are 1,334 foundries employing 144,000 people that use sand from
the Lake Michigan area. The foundry business, which depends upon sand for making cores and
molds, is the one of the 20 largest industries in the USA, in terms of goods and services
produced.
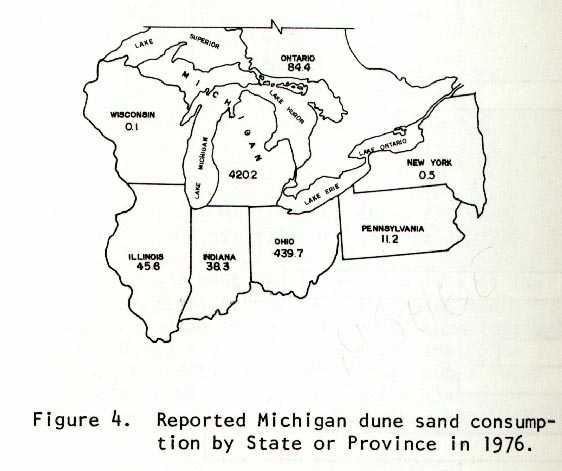
Source: J Lewis,
Michigan
Geological Survey Division Circular (#11), 1975
SAND MINING AND THE ENVIRONMENT
The Lake Michigan Federation, a Muskegon-based environmental group, has
been actively involved in the fight to save Michigans sand dunes for the past six
years. In 1976 there were 15 active mining sites covering 3,228 acres. By 1999 that number
had grown to 4,848 acres at 20 sites. About 46.5 million tons of sand have been removed
since the passage of the dune protection act. The sand is used for making car molds,
trains and airplane parts. The sand along the shore is useful to the auto industry because
of its composition. It is unique in its purity. Quartz is the primary ingredient.
The depletion of the dunes also has negatively affected wildlife, such
as the Piping Plover bird, which is on the federal endangered species list. Only 23 Piping
Plover nests were accounted for in Michigan in 1996, many of which nest in the dunes.
CONCLUSIONS
Michigans industrial sand mining industry faces an uncertain future. This industry,
like many other extractive industries, is being subjected to increasing public and
governmental pressure to severely limit or stop its sand mining operations, especially
along Lake Michigans shoreline areas.
Dune sand is preferred by industrial consumers because of its chemical
and physical properties, ready availability, and agreeable price. Sand mining operators
prefer to quarry dune sand (below) because it is found in large volumes and is relatively
free from excessive contamination and overburden. Compared to other sand sources it
requires less processing, is more easily mined, and is close to bulk transportation
facilities. The mining of thinner, inland sand deposits usually require additional
processing, more handling, and disturbs large areas. The additional consumption of time
and energy to carry out all of these operations contributes to increased costs.
With the increased concern about sand mining in Michigan we are now
forced to make a decision: 1) Should all dune sand mining be halted along the Great Lakes
shorelands; 2) Should dune sand mining be allowed to continue unabated as in the past; or
3) Should we seek a compromise to these opposing positions?
The elimination of sand mining within the Great Lakes shorelands, is
supported by growing numbers of ecologically minded citizens. They contend that the dunes
and their fragile ecosystems should not be destroyed as they are vital to the ecology of
the area and invaluable educational and recreational assets that should be preserved
intact for future generations to study and enjoy.
The continuation of present mining practices is supported by equally
concerned industrial opponents. They contend that Michigan is an industrial state and that
industrial sand is the backbone of all basic industrial manufacturing in the state.
Without dune sand our automotive and associated manufacturing industries would be forced
to shut down or seek more costly alternatives.
Much of the text and imagery on this page is from a 1975 Michigan Geological
Survey Division Circular (#11), by J. Lewis.
This material has been compiled for educational use only,
and may not be reproduced without permission. One copy may be printed for
personal use. Please contact Randall Schaetzl (soils@msu.edu)
for more information or permissions.
|