CLAY AND SHALE
Clay is an important raw material in the manufacture of bricks; in fact, it is the main
raw material in such manufacturing. Michigan produces many millions of tons of
bricks annually. The clay for these bricks comes from two sources: clayey sediments
laid down in glacial lakes, and shale bedrock. The
map below shows where such locations exist in the state.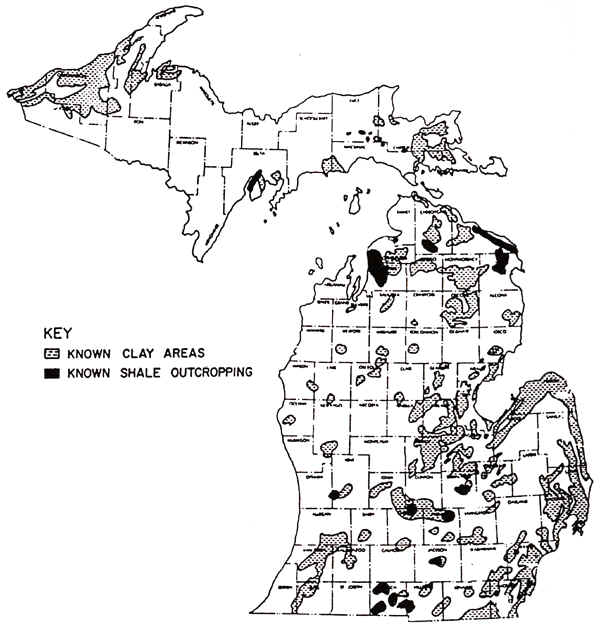
Source: Unknown
Shale was originally deposited in shallow waters of the Michigan basin, as clay. It
eventually hardened into shale. Clays laid down by the receding ice sheets primarily
were deposited in the deepest waters of proglacial lakes.
The black Mississippian shale, the
Antrim shale, the green Ellsworth shale, and the blue Coldwater shales are very useful in
the manufacture of cement, brick and tile. Quarries are worked in them in Alpena,
Charlevoix, Antrim and Branch counties.
The mining, production and uses of cement, clay and shale are
quite similar. Cement is made from shale or clay, and limestone. The term
"cement" is most often used to refer to Portland cement. Portland cement, when
mixed with sand, gravel, and water, makes concrete, which is an essential element of the
construction industry. Portland cement accounts for more than 95% of all cement produced.
To make Portland cement, clay, shale and limestone is ground to a powder and baked in a
kiln. The baked mixture forms clods (clinkers), which are then ground up and mixed with
gypsum. Most of the raw materials are mined in open pits. Michigan traditionally ranks in
the top five states in terms of cement production. One of the largest cement plant in the
state is in Alpena. Making Portland cement requires lots of heavy raw materials and a
tremendous amount of energy.
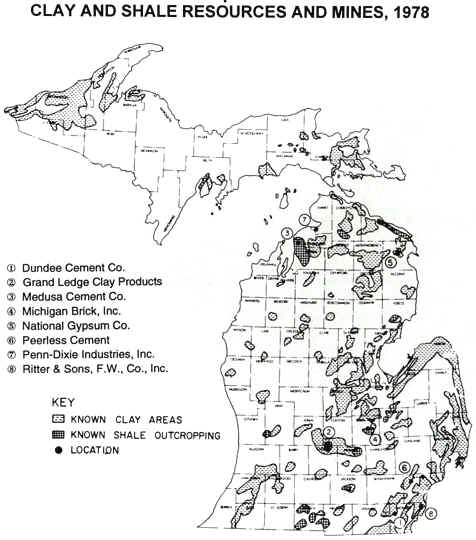
Source: Unknown
Clay is also used to make pottery and tile (clay pipes). The city of Grand Ledge
has a history of manufacturing based on clay as a raw material.
Until it closed, Grand Ledge Clay Products remained an old-time
industry, retaining many of the methods and equipment that were used decades ago. For the
first 35 years of its operation, Grand Ledge Clay Products manufactured conduits for
underground telephone wires. Chicago was a prime market for that product, and many a
street in Chicago still has Grand Ledge tile underneath it. These telephone
conduits---hollow, pipe-like tiles, see below---were also used as building materials. The
plants horse livery, built in 1908 and later used as a garage, had mortared conduit
tile for its foundation and walls. Other houses and buildings in Grand Ledge also were
made of the tiles whose ends were often filled in with cement.
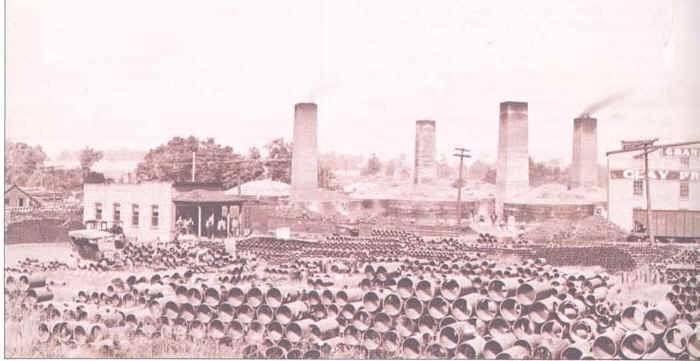
Source: Image courtesy Michigan History Magazine
In 1937 a fire razed the factory building, destroying the molds that
were used to make the conduits. Then the market for clay drain tile declined, and the
company shifted production to agricultural drain tiles, chimney tops and sewer pipe
fittings.
The process used to produce tiles has not changed much over the years.
Nearly all the raw material----actually a shale, not a clay----was mined from the
property. In the early days, horses pulled railway carts full of the soft rock from open
pits to the factory; later, a small locomotive did the job. The chunks of shale were then
ground and sifted into a fine granular powder that was mixed with water to form a soft
clay. The clay was then forced down through a bore and extruded through a die to form
tiles.
The fragile, "green" (unbaked) tiles were dried and then
transported to the kilns. Firing took from 50 to 140 hours, depending on the thickness of
the tiles. Vitrification occurred at 1860-1940 degrees F, the temperature at which clay
particles liquify slightly and are thus bonded together.
For many years, salt was added during firing to create a glaze on the
tiles that made them less permeable to water. However, testing proved that salt also
weakened the tile. After the conversion to gas firing, which allowed more precise control
of firing times and temperatures, better vitrification could be achieved, and glazing was
no longer needed.
Grand Ledge Clay Products was not the only such industry in Grand
Ledge. Across the street, the American Sewer Pipe Company (later the American Vitrified
Company) took advantage of the rich subsurface deposit from which fine clay products could
be made. That deposit, called the Saginaw shale, is an extensive formation of soft,
layered rock that was deposited in the quiet waters of an ancient ocean. These rocks are
well known for preserving fossils of the prehistoric ferns and trees. Coal, the
concentrated carbon residue from the partial decay of those swamp plants, is also found in
the area.
Saginaw shale is a mixture of fine silt and sand particles. Although
harder to work with than most deposits used in the clay industry, it made an extremely
fine product. With a large, rich deposit of high quality raw material and decades of
successful operation, why did Grand Ledge Clay Products close? Part of the reason can be
stated in one word----plastic. Plastic sewer pipes and drain tiles have largely replaced
their clay counterparts. Lansing and Flint were two of the last cities in Michigan to
still use clay sewer pipes.
Because of the slackening demand for clay sewer pipe and tiles,
production at Grand Ledge Clay Products in the late 1960s and early 1970s moved to chimney
flue liners. In the early 1980s, a series of new plant managers introduced the manufacture
of veneer tiles and paving bricks. Although the spotted bricks were very popular, it took
some time to discover that architects were the key customers for them. By the time that
discovery was made, the companys capital was exhausted. Rather than renovate the
plant, the stockholders decided to close and liquidate its stock.
The presence of Grand Ledge Clay Products will not be easily erased.
Acres covered with hills of unused clay form a desolate, eerie landscape behind the
factory---a miniature badlands. The stream beyond flows over pottery shards, so much a
product of this land that they seem to belong there. Near the stream, huge old sewer pipes
have been captured like spools on a stick by 20 year-old poplars growing through their
center.
Some of the images and text on this page were taken from various issues
of Michigan History magazine. This material has been compiled for educational use only,
and may not be reproduced without permission. One copy may be printed for
personal use. Please contact Randall Schaetzl (soils@msu.edu)
for more information or permissions. |