EARLY IRON MINING
The Onset of Mining.
To determine the land boundaries that would properly establish mining
locations, it was necessary that a linear survey be made by federal authorities. Such a
survey party, headed by US surveyor William Austin Burt, discovered the first iron ore
deposit of the Lake Superior region-near present-day Negaunee, Michigan. The survey party
had stumbled into the heart of one of the richest iron ore districts in the world.
On September 19, 1844, near Marquette Countys Teal Lake, William Austin Burt and his
survey crew watched as the needle of their compass fluctuated wildly. Burt had no
idea that this accidental discovery would provide the foundation for Americas
Industrial Revolution when he called out....."Boys, look around and see what you can
find."
On the heels of the surveyors came the government geologists. The iron
formation in the Marquette Iron District commonly consisted of thin layers of silica-rich
rock, such as slate or chert, alternating with thin layers of almost pure iron
minerals-mainly magnetite, specularite and hematite-"whose purity and magnitude are
unrivaled." Foster and Whitneys geological map showed iron formations occurring
in a belt eight miles across at its widest and extending west for some thirty miles to
Lake Michigamme. Here a branch extended southward eight miles along the Michigamme River.
The prospectors and miners followed the government geologists. The
first iron mines in the Marquette District were in Negaunee and Ishpeming. Initially, only
the near-surface concentrations of magnetic hard ore were discovered and extracted. The
early mines were relatively small, shallow open pits (below), which often were soon
exhausted. By 1875 some of the near-surface ore bodies were being followed underground.
Early mining operations were carried on primarily by manual labor. After drills and
hammers created holes for blasting, the blasted ore was then loaded into wagons that were
hauled by mule or horse to the railroad.
Development of the district began slowly but was hastened by the
opening of the Soo Locks in 1855 and the building of railroads from Lake Superior to the
mines during the late 1850s. Other key factors in the development of the district were the
rapid expansion of New England manufacturing plants and the increased demands for iron
caused by the Civil War. As a result of this need for iron, the entire Marquette District
was eagerly explored with test pits. The number of new mines proliferated. By 1873 annual
iron ore production from the Marquette District reached 1,000,000 tons.
Some 60 km south of the Marquette District were the three segments of
the Menominee District, the second great iron-producing area to be discovered in the Upper
Peninsula. But development of the district was impeded by the lack of cheap
transportation. Only when a rail line was built in 1877 to carry the ore from the mines to
Lake Michigan docks could the ore in this area be mined profitably.
Throughout the early phase of production, the ore was smelted on the
mine site, using charcoal from local hardwoods, and then shipped via the Great Lakes. The
needs of the smelting operation, combined with the activity of the lumbermen, succeeded in
stripping the Upper Peninsula of most of its timber. It was perhaps fortunate, then, that
during the 1870s, the center of the iron and steel industry moved to the markets,
smelters, and coalfields of the Ohio Valley.
During the 1870s high-grade ore was so abundant and mining and furnace
methods were so crude that only the hard specularite and magnetite ores, mined in the
Marquette District, were considered valuable. The soft hematite, which later came to
comprise the bulk of the ore shipped from the Lake Superior area, was contemptuously
called Lake Superior mud. By 1874, with the employment of more sophisticated smelting
procedures, some furnace operators began using the more abundant, soft hematite ores.
Transportation of the ore to Lake Michigan shipping docks, closer to
the blast furnaces of Gary and Chicago, also proved difficult. Only when a rail line was
built in 1877 to carry the ore to the Great Lakes shipping docks could the ore be mined
profitably.
At the west end of the Upper Peninsula lies the Gogebic District, the
third great iron ore region to be discovered in Michigan. Here again, a lack of
transportation and the general disdain for the soft hematite ores delayed the development
of the Gogebic District into an ore-producing area until 1884.
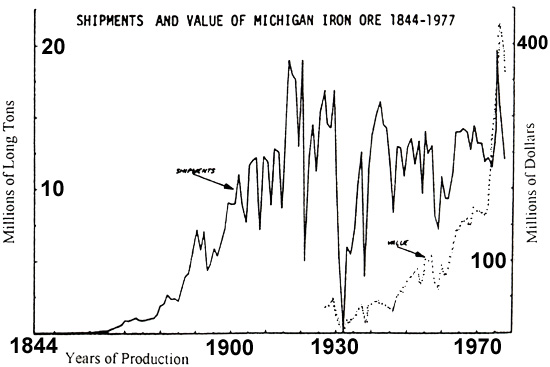
Source: Unknown
Finding the ore.
When prospecting for iron ore, attention was first paid to outcropping
rocks to determine whether a region contained the iron formation. Once in proximity to the
iron formation, the prospector looked for an outcropping of ore, or for signs that ore
might be nearby, such as the presence of a boulder containing ore, a red, hematite-rich
soil in the roots of a fallen tree, or the deflection of the compass needle by local
magnetic attraction. Because bedrock is often buried, the prospector habitually examined
the banks and beds of streams and the cavities under overturned trees for bedrock
exposures.
When an iron ore deposit was found, careful work was necessary to
determine the quantity of ore present (defined by the deposits length, width and
thickness) and its richness. The majority of mining-company failures occurred because
their iron ore deposits were not rich enough to be mined profitably. A lesser number of
failures happened because the ore deposit was too small, even though the ore was high
quality.
Only those parts of the iron formation where some natural process had
concentrated the iron ore to at least 50% of the total rock to be removed could be mined
at a profit. About 6% of the iron-formation area met this requirement. These rich, natural
concentrates, called direct-shipping ores, were considered the only profitable ores until
the 1950s.
To determine an ore deposits boundaries, the area was first
roughly mapped, noting all outcrops, then traversed with a dip needle to trace the
deposits underground outline. The dip needle is a hand-sized, circular box with a
glass top and bottom that allows the needle movements to be easily seen. The needle is
counterpoised, resting horizontally when there is no local attraction but dipping in a
vertical plane when attracted. The direction in which the dip needle points is due to the
combined magnetic effect from both the earth and the local ore deposit. Since magnetic ore
attracts the needle at the same distance with equal strength whether covered by rock,
earth, air or water, this instrument was of great service to prospectors. The dip needle
was successful in locating and tracing the boundaries of iron ore deposits because most
iron ore was magnetic enough to produce an appreciable deflection in an ordinary compass
bearing.
The intensity of a local attraction depended upon the amount of
magnetite in the rock and was measured by the number of needle vibrations in a unit of
time. While a dip or defection was frequent, it usually did not signify a profitable iron
ore deposit since there were many more lean ores than rich ones.
The first iron ores usually discovered were hard magnetite and
specularite. These dense ores were more readily found because of their resistance to
erosion, their tendency to form outcrops and their ability to magnetically deflect compass
needles. However, most of the ore mined in the Michigan districts has been the soft
hematite ores. Although more abundant, this earthy ore was more susceptible to erosion and
tended to recede into the subsurface, becoming harder to find. The location of subsurface
iron ores was difficult to predict. Folds, faults and igneous intrusions caused the ore to
appear capriciously in pockets within the iron formation.
Today the mine headframe (shafthouse) still stands as a local monument to this glorious
era in Michigan's mining past.
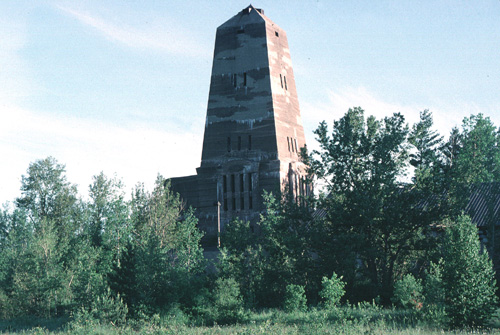
Source:
Photograph by Randy Schaetzl, Professor of Geography - Michigan State University
By the turn of the century mines in Ishpeming were producing more than 2 million tons of
ore per year. Shaft mines like this one were extremely prosperous and productive during
the early 20th century.
Click here to continue on with this page. There's a lot
more!
Some of the images and text on this page were taken from various issues
of Michigan History magazine.
This material has been compiled for educational use only, and
may not be reproduced without permission. One copy may be printed for personal
use. Please contact Randall Schaetzl (soils@msu.edu)
for more information or permissions.
|