GYPSUM
During the Paleozoic Era, beginning about 600 million years ago and ending about 230
million years ago, seawater invaded the Michigan Basin at least six times. As the seas
receded and evaporated, rock and mineral deposits such as halite (rock salt), gypsum
(calcium sulfate with water), liquid brines, petroleum, lime, clay, sandstone and coal
were left behind. The fifth of these seas, the Mississippian, was responsible for
Michigans gypsum deposits, which are among the richest in the world.
Gypsum is a non-metallic mineral, found in rock form. It is composed of
79.1% calcium sulphate and 20.9% water, by weight. Chemists call it Hydrous Calcium
Sulphate, and as there is one molecule of calcium sulphate combined with two molecules of
water. It has the chemical formula CaSO42H20. By volume this works
out to nearly 50% water in the mineral structure. This water however, is perfectly dry,
and is known as "water of crystalization". It could be compared with ice, which,
too is water in crystaline form, but there is this an important difference; ice will melt,
or change to water, when it is exposed to a to temperature above 32 F.
Water of crystalization, in gypsum, does not change until it is subjected to heat above
212 F but at that temperature the water of crystalization
changes form and becomes water vapor and is driven off from the gypsum just as steam is
driven off from water at 212 F. Gypsum, an evaporite rock, formed at the base of the shallow Michigan basin as it dried up, leaving the CaSO4 H2O
deposits behind, as gypsum.
In absolutely pure form, gypsum is white. However, gypsum normally
contains impurities whose presence makes the rock appear gray, brown, pink, or even almost
black.
ORIGIN OF GYPSUM DEPOSITS
Gypsum is found in many parts of the world. Gypsum deposits lie in flat beds of about six
to eight feet in thickness, and are often inter-layered with limestone or shale. Gypsum
deposits were formed millions of years ago when salt water oceans covered most of the
earth, and as they receded, may inland "dead" seas were formed which, as
evaporation continued, became more and more salty. As those salts precipitated, they
formed various compounds in turn, one of which was gypsum. As millions of years passed,
these salt deposits combined with decayed vegetation and other minerals, and eventually
the result was stratified rock, with layers of gypsum and layers of limestone alternating,
the whole covered over with many feet of glacial deposits.
Gypsum is produced commercially from open pit quarries near
Tawas City and Alabaster in Iosco county and from underground mines near Grand
Rapids. Gypsum deposits are located in the center of the Michigan
basin. It is only mined at places where the gypsum is near the surface, while at
others it is buried by more than 1200 feet of rock (see map below). Gypsum beds are
seldom more than 20 feet in thickness. Near Grand Rapids, gypsum of the Michigan
Formation are mined extensively, for they are very near the surface in that area.
The map below shows where some of the gypsum units in the Michigan Formation are
located, and the stratigraphic column below shows where the Michigan Formation fits into
the rock layercake that is the Michigan Basin.
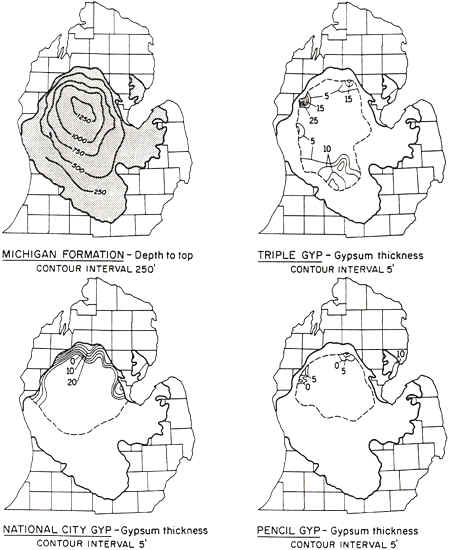
Source: L.M. Sommers, Michigan: A Geography (1984).
The maps below show where the Michigan Formation (dark gray), with its rich deposits of
gypsum, occur as the uppermost rock unit.
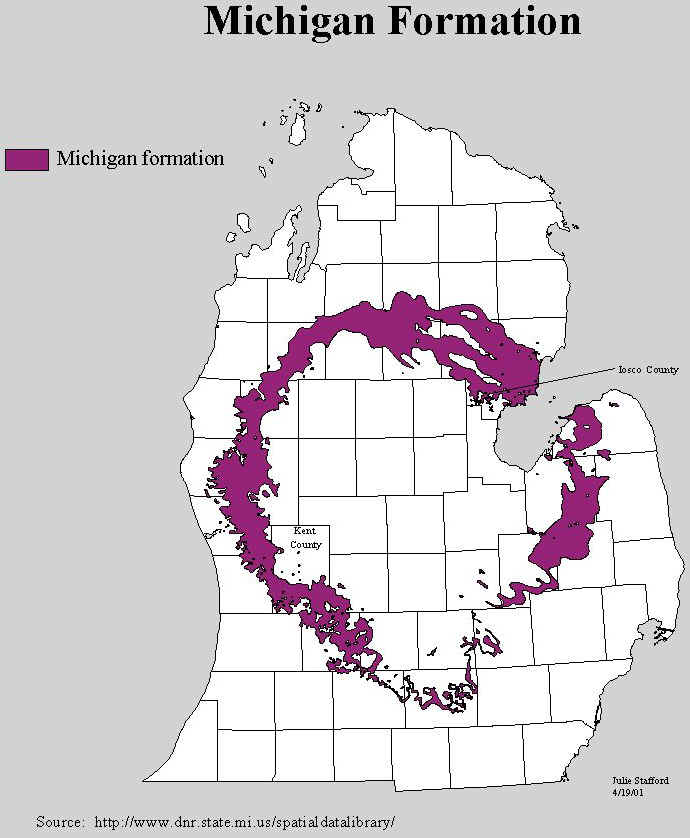
Source: Michigan State University, Department of Geography
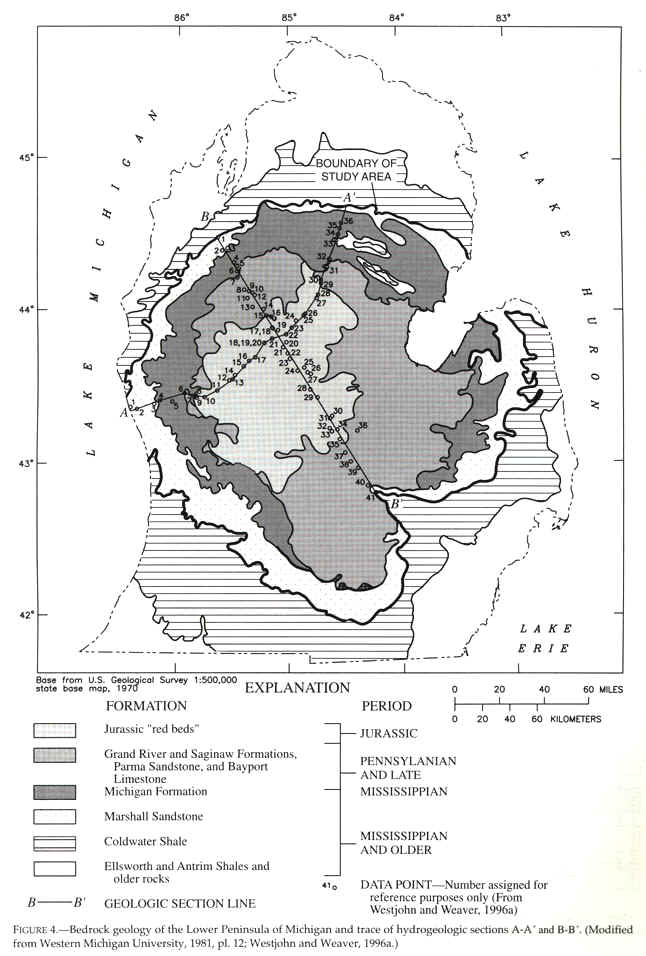
Source: L.M. Sommers, Michigan: A Geography (1984).
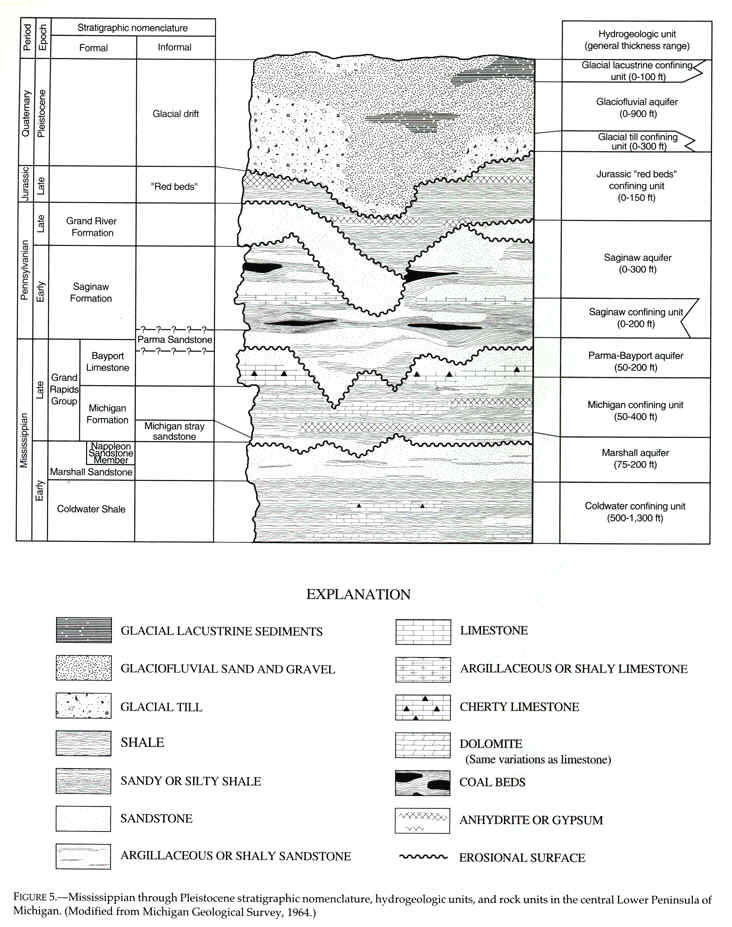
Source: L.M. Sommers, Michigan: A Geography (1984).
FIRE-PROTECTION QUALITIES OF GYPSUM
The fact that gypsum contains so much water which is released when exposed to intense heat
is the basic reason why building materials made of gypsum offer fire-protection. When a
wall or ceiling coated with gypsum lath or plaster is exposed to ordinary room
temperature, nothing happens, but should the contents of a room catch fire, the heat would
quickly exceed 212 F. However, no matter how hot the fire,
the temperature of gypsum walls and ceilings will not exceed 212 F
because at that temperature the water in the gypsum will start to vaporize and be released
as steam. Until all the contained crystalized water has been driven off, the gypsum will
remain at 212 F, protecting the wooden framework of the
structure, or whatever flammable materials the gypsum may be covering.
Of course this protection lasts for only a limited time, depending upon
the thickness of the gypsum, also the gypsum is destroyed in the process of calcination
that takes place. However, countless buildings have been saved from destruction by the
fire-retarding action of the gypsum, which either permits the fire to burn out without
damaging the structure, or gains precious time for action to be taken to fight the fire
and save lives or property.
EARLY USES OF GYPSUM
Gypsum and its products have been known and used from earliest times. The ancient
Assyrians called this beautiful rock Alabaster, and used it for sculpturing. Five thousand
years ago the Egyptians had learned to make plaster from gypsum; they lined the walls of
their palaces, and their tombs with it, and some of this earliest gypsum plaster has been
found inside the great Pyramids, unchanged after 50 centuries. It was the ancient Greeks
who named this magic mineral "Gypsos", from which we have derived the name
Gypsum. There is another form of gypsum which is clear and transparent, in layers like
mica. This was used, many centuries before glass was invented, as windows in the old
temples. The Greeks named it after their Moon Goddess, "Selene", and today we
still call it "Selenite".
No one knows just who discovered the unique property that makes gypsum
so valuable. However, some early experimenter found out that gypsum rock can be ground up
to a powder and heated in a kettle (calcined) until most of its water content is removed.
When water is added to the resulting white powder, it forms a pliable, plastic mass
(Plaster of Paris) which can be molded into any desired shape, after which it will harden
and retain that shape. When the hardening has been completed, the substance recrystallizes
and technically has then been restored to its original rock-like state.
THE ROCK NOBODY KNOWS
If you were given a chance to win a jackpot by correctly naming a material that was used
in the pyramids and in your toothpaste; that helps peanuts grow and makes movie snow; and
that is used in mushroom beds and the walls of your house, chances are at least 100 to 1
that the quizmaster would holler "Sorry, your time is up," before you could say
"hydrous calcium sulphate."
But, dont feel badly.
Even though more than 12 1/2 million tons of gypsum were used in the
USA last year, and even though the average person is surrounded by gypsum products from
dawn to dusk, from the cradle to the grave, people do not know much about gypsum.
Gypsum can be ground up and "boiled" (calcined) at a
comparatively low temperature until 75% of its moisture content has evaporated. When that
happens, the rock becomes a fine powder, commonly known as Plaster of Paris. By returning
the water to the powder, one can make a pliable mortar that can be formed into any shape
and hardened. Gypsum is the only natural substance that can be restored to its original
rock-like state by the addition of water alone.
When this great secret of nature became common knowledge, it
didnt take long to put it to work. How well it has served us through the centuries
can be seen from a listing of a few of the ways in which you come in contact with gypsum
during an average day. Most of the fixtures in your bathroom were made of clay formed in a
mold of gypsum plaster and chances are that the tile on the wall is set in another type of
plaster. At the breakfast table, you use plates, cups, and saucers which were shaped on or
in a gypsum mold. So were the sterling silver handles of your knives, forks, and spoons.
When you settle back after breakfast for a second cup of coffee, you light your cigarette
with a match which has gypsum in its head. Of course, the walls and ceilings in your home
almost certainly are made of gypsum lath and plaster or gypsum wallboard. This guarantees
your comfort and safety because gypsum is strong stuff and, whats more, fireproof.
When you leave home for work you step on sidewalks made of Portland Cement which contains
gypsum to regulate the setting time. Maybe your walk is covered with chalk marks from the
game the children were playing the night before. But, of course, they werent made by
"chalk" at all but by a molded stick of, you guessed it, soft gypsum plaster.
Many of the streets and highways you travel daily also contain gypsum. Your car windows
are made of plate glass which was held in a bed of gypsum during the polishing process.
Many of the small metal gears, the instrument bases and other metal parts on your car were
cast in gypsum molds by a process that was largely perfected during World War II. If this
happens to be your day to go to the dentist, hell tell you that he uses a gypsum
dental plaster mold in which to cast a bridge. Your doctor uses gypsum when he builds
splints for broken limbs from a gauze impregnated with orthopedic plaster.
Everybody uses the rock nobody knows. Benjamin Franklin, the great
experimenter, was one of the first to introduce it in this country when he used ground raw
gypsum, called land plaster, on his farm. Today, 188,000 tons of land plaster are used in
the United States each year (see ad below).
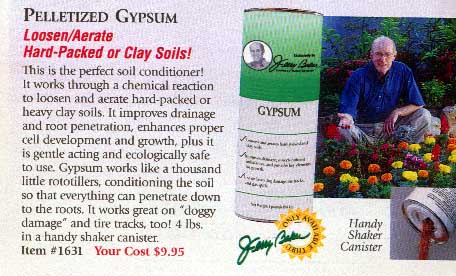
Source: Image courtesy of Randy Schaetzl, Professor of Geography - Michigan
State University
Hollywood uses gypsum to represent snow. Whether for a white Christmas or a raging
blizzard. Most of the spectacular movie and TV sets, too, are formed from gypsum plaster.
At the end of the glamour scale, gypsum is mixed with manure used to make mushroom beds.
By far the largest part of the gypsum used in this country goes into
wallboard and lath for our homes. These gypsum "boards" are formed by
sandwiching a core of wet plaster between two sheets of heavy paper. When the core sets
and dries out, the sandwich becomes a strong, rigid, fireproof building material.
Manufactured in unbelievable quantities on continuous machines almost a quarter mile in
length, gypsum wallboard and lath, are among the most important materials used in housing.
THE MIRACLE OF GYPSUM
Gypsum's main use is in the construction business, as wallboard, or "drywall".
"Drywall" come in large sheets, and is used to coat the walls of many,
many houses and office buildings. Drywall is composed of about a quarter inch of
gypsum between two sheets of paper ("lath"). But what makes the gypsum
plaster adhere to the paper and wood (termed "gypsum lath")? The
surface of the lath appears relatively smooth, yet when the wet plaster is mixed with
twice its weight of sand and applied to lath, a pull of almost half a ton per square foot
is required to remove it. About 1/5 the weight of gypsum rock consists of water,
chemically combined in its crystalline structure. In making plaster, the rock is cooked or
calcined until its water content is reduced to1/4 the original. The answer to the above
question is, then, this: When the plaster is applied to lath the solution of plaster is
absorbed into the pores of the lath paper, and when the gypsum crystals grow they
interlock with the lath/paper to establish a tenacious bond.
As of 1978, there were five major companies mining gypsum in Michigan; these are shown
below. Note the locations of these companies/mines--many are located near the water,
so that the low-value gypsum can be transported in bulk by ships.
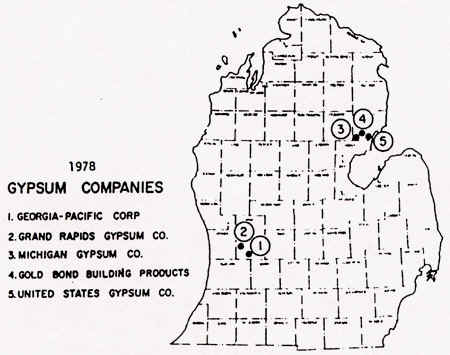
Source: Unknown
Although the data below are a bit old, they do give an idea of the value of gypsum to
Michigan's economy, and show that Michigan's gypsum production has steadily increased
during the 20th century. If any rock or mineral product could be thought of as
"unlimited", it would be the gypsum deposits in the United States. It is one
material of which we could never run short. Deposits are found in two (2) principal belts
- the first starting in Southwestern Texas, running up through Central Kansas, across Iowa
and into Southern Michigan, then turning Southeast along the Northern edge of Ohio and
crossing the Niagara River into New York State. The second belt starts in the Imperial
Valley of California, goes up through Nevada and fans out into Utah with a thin extension
into Montana. In places, these deposits are 150 to 200 miles in width.
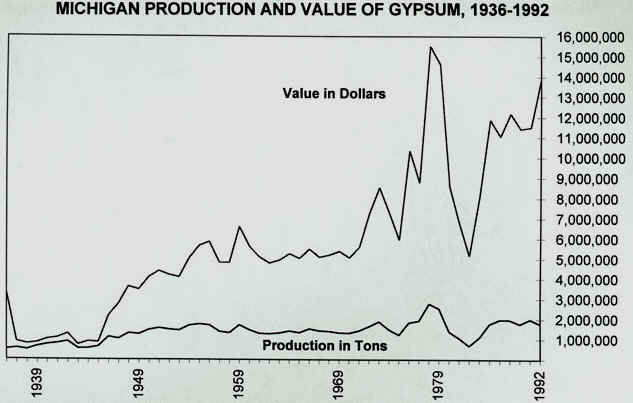
Source: Unknown
HISTORY OF GYPSUM IN GRAND RAPIDS, MICHIGAN
In 1827, when Grand Rapids was little more than a tiny settlement, an Ottawa Indian
discovered a rock outcrop where Plaster Creek (an appropriate name, huh?) enters the Grand
River and took a sample of the soft, sugary material, which was eventually identified as
gypsum. Little more notice was taken until 1838, when Douglass Houghton, Michigans
first state geologist, arrived in Grand Rapids to select the site for a salt well and
reported afterwards about the abundant presence of gypsum. At the time, salt was regarded
as the up and coming industry for the village, but major difficulties with its extraction
rapidly dimmed its light, and interest in gypsum brightened.
The areas first commercial gypsum operation began in 1841 when
Daniel Ball and Warren Granger built a mill on Plaster Creek and turned out 40 tons of
product (gypsum) in a single week. Eight years later, Richard Butterworth opened a quarry
on the west side of the river, and the establishment of two more quarries extending into
the hillsides near the river quickly followed. In 1860, these holdings were incorporated
into another operation, the Grand Rapids Plaster Company, and the combined enterprise
became known as the Eagle Mills Plant. Eventually, there were 13 separate gypsum mine
operators in the Grand Rapids area, and by 1890, the citizens of Grand Rapids viewed the
gypsum quarries as a "mine of apparently inexhaustible wealth to our city."
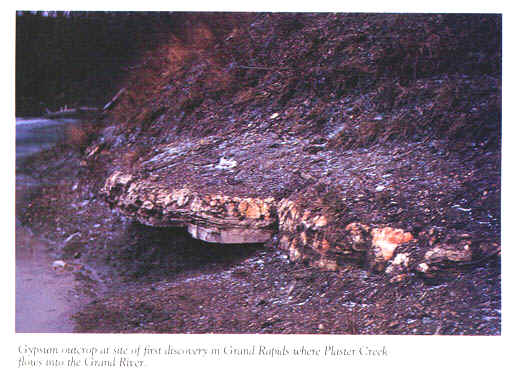
Source: The Grand Rapids Press
From the beginning, the demand for gypsum was great. In the early days
of gypsum mining, farmers drove their horses and wagons as far as 100 miles to purchase
supplies of "land plaster" for use as fertilizer, or soil "sweetener"
as it was called at the time. The primary use of gypsum through this period was as land
plaster and fertilizer until about 1880. The coming of the railroad to Grand Rapids in
1865 expanded the market for locally mined gypsum all the way to California. Gradually,
the uses for gypsum increased to include stucco and ornamentation for building exteriors
and plaster for interior walls. By 1889, 2/3 of the output was used in finishing interior
walls and ornamental work. The first wallboard operation was established approximately
1900 by the Sackett Wallboard Company, a hand trowel rock lath operation. By 1890,
Michigan was one of the leading producers of gypsum and for the last 40 years has ranked
second among the states in domestic production.
Although it was later discovered that slabs of gypsum used as building
facings disintegrated rapidly after being exposed to the elements, this very softness made
for easy carving into bowls, vases and sculpture.
In 1893, this may have spurred William Powers to begin mining gypsum on
his west-side Grand Rapids property. Unlike other operators of the time, who tunneled for
mineral, Powers opened the citys first shaft-mining operation. While his venture
into a 12-foot layer, 60 feet below the level of the riverbed, was short lived, the exact
site of his "digs" aroused intense interest nearly 75 years later when the city
became involved in urban renewal and redevelopment along the riverbank.
Over the years, many of the areas smaller gypsum mines were
consolidated into larger holdings, and soon after the turn of the century, the remaining
individually owned enterprises were purchased by major companies that brought with them
modern equipment and methods. By the late 1920s, the horse-drawn mine cars of a previous
era were gone. Gone also were the associated mushroom industry, which flourished in the
dark dampness beneath a layer of fertilizer supplied by the horses.
In 1946, the Alabastine Mining Company mine in Wyoming, which had
recently closed, gave rise to an entirely new enterprise. Seeing great potential in the
constant temperature (54�-55� F) and 95-97 percent humidity, Bert Kragt and his family
bought the old mine, cleaned out some of the six miles of abandoned tunnels and
established the Michigan Natural Storage Company some 80 feet underground. Originally used
to store foods such as eggs, nuts, cheese and potatoes, the facility today, grown to
45,000 square feet and equipped with temperature and humidity controls for specialized
storage needs, provides a safe and comfortable home for microfilm and computer records as
well as food. The companys deep-freeze rooms also play temporary host to most Grand
Rapids-area Thanksgiving turkeys before they make their way to local supermarkets.
The room and pillar mining method leaves considerable rock in place as
a natural support. Ventilated by fans that circulate fresh air, the rooms and tunnels are
about 100 feet below the surface. Diesel-operated machines drill a specific pattern of
blast holes in the end of each working side tunnel or "bench." Front-end loaders
transport the blasted rock to the main tunnel for delivery to the plaster mill where it is
processed. Current mine output of about 600 tons per day requires only two maintenance
workers and a production crew of five.
Over the years, Michigan has consistently ranked first or second in the
United States in production of gypsum, and the deposits are vast. This versatile mineral
touches our lives every day and promises to be an important part of our future.
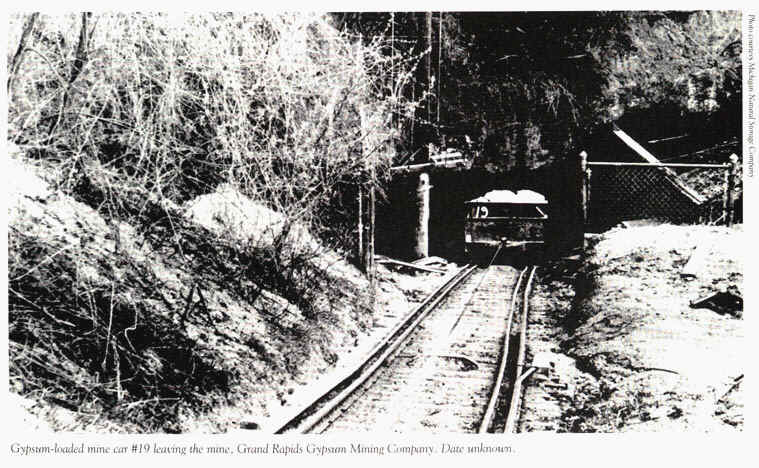
Source: The Grand Rapids Press
In 1838, Bela Hubbard, along with Dr. Douglass Houghton, discovered
gypsum in the mouth of the Aus Gres River in Arenac County on the west side of Saginaw
Bay. In 1862, the first mill was constructed at Alabaster, Michigan. Major mining in the
Bay area at Alabaster began in the 1860's, and has since become the most important gypsum
mining area in Michigan. This material has been compiled
for educational use only, and may not be reproduced without permission. One
copy may be printed for personal use. Please contact Randall Schaetzl (soils@msu.edu)
for more information or permissions.
|