SALT BRINES
Above and within the Coldwater shales is one of the most interesting of our
rock bowls-the Marshall sandstone. The rim of the Marshall comes to, or is near, the
surface in many places from the tip of the Thumb where it is carved to interesting
scenery, through Huron, Jackson, Calhoun, and Ottawa counties. In the early day many
quarries were opened in it and the sandstone used for building purposes. One of our ghost
towns is Grindstone City, Huron County, where once a flourishing industry produced the
largest and finest grindstones, scythestones, and honestones in the world. Artificial
carborundum, however, killed that industry. But when particularly fine grind-and
hone-stones were needed the quarry was occasionally operated.
Near its buried edges the Marshall is a major groundwater aquifer and
is the source of the water supply for many cities (see map below).

Source: Unknown
Deeper, toward the center of the basin, the groundwater in the Marshall gradually seep
down the slopes toward the center of the basin. Along the way it dissolves mineral matter
in the rock and when it reaches the bottom of the bowl (Midland County) and meets the old
sea water of Mississippian time imprisoned there, it is a very bitter water carrying much
chlorine, iodine, magnesium, sodium, and other salts and minerals in solution.
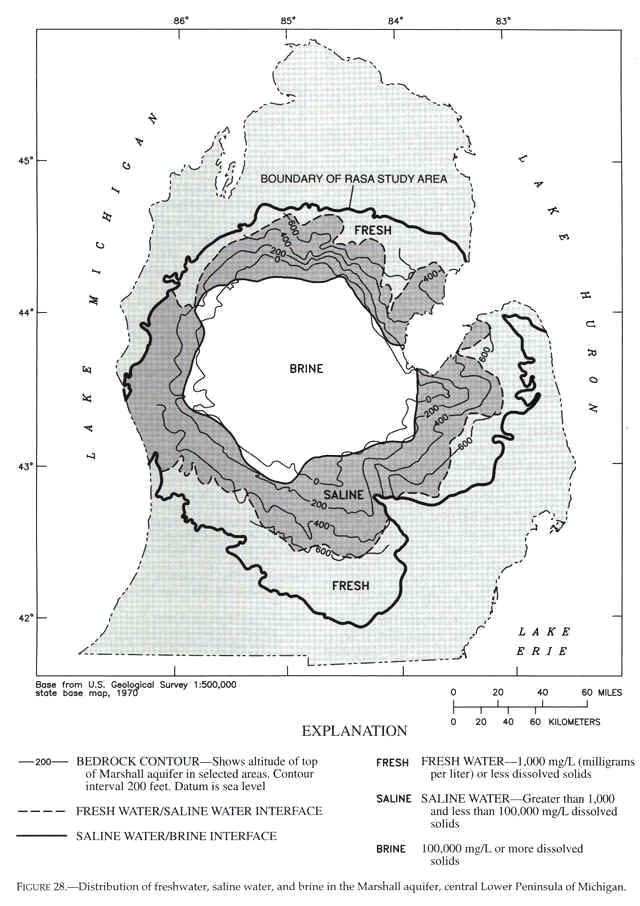
Source: Unknown
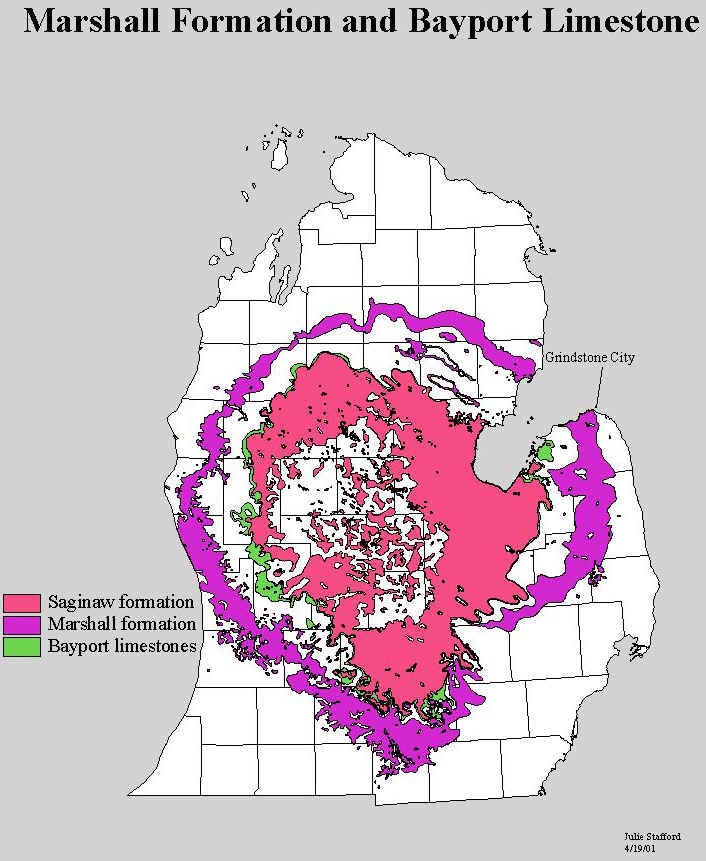
Source: Michigan State University Department of Geography
This brine is the source material for a great chemical industry Dow Chemical, among others.
The manufacture of salt in the Saginaw Valley was closely related to
the lumber industry. The East Saginaw Salt Manufacturing Company, the first commercial
producer of salt in Michigan, used refuse from local sawmills as fuel in its kettle
evaporation process. And when improvements in technology, such as the grainer (shallow
tank) and open pan processes, replaced the older kettle process, sawmill refuse (wood
chips, sawdust, etc.) was burned to make steam for the mill, and the exhaust steam was
used by the salt companies in the grainers.
Although the Bay City Salt Manufacturing Company started drilling a
brine well in 1860, the first actual production came from the Portsmouth Salt
Manufacturing Company the following year. Both companies were located in Bay County. Two
years later, in 1863, a salt block (a salt factory using an evaporating process) was built
and the industry spread throughout the area. Since salt manufacturing depended on the
lumber mills for fuel, the salt blocks closed as the sawmills moved out of the locality.
Today, only the Huron County Road Commission, which used salt for dust and ice control,
operates brine wells in the area.
Following the northward movement of the lumber industry, salt works
spread into Iosco County. Grant and Son built the countys first salt block at East
Tawas in 1872. Later, blocks were erected at Tawas City, Oscoda and Au Sable. But all of
these were short-lived, and no salt production has been reported in the area since the
turn of the century.
The salt industry was also tied to the search for oil in Michigan. In
1881 oil drillers in Manistee County failed to locate oil, but discovered a 10 meter thick
salt bed. The salt industry that began then remains active today, with both the Hardy and
Morton salt companies currently operating plants that produce evaporated salt.
Today, in the Downriver communities of Detroit, chemical industries
pump water down into a slab of solid salt and force back brine (see below). Brine
mining is also done at Ludington and Manistee.
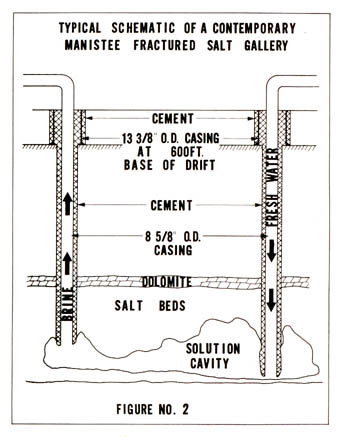 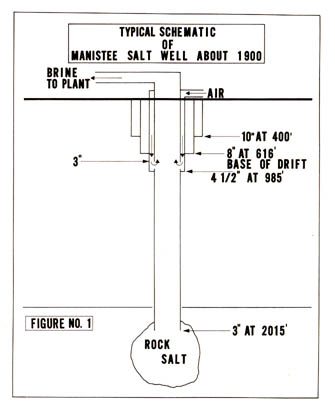
Source: Unknown
The salt is used in countless industries, in the manufacture of chemicals, preservation of
meats and food products, curing of hides, and for highway stabilization and control of
snow and ice.
About the only thing that Metropolitan Detroit doesnt produce in
the way of salt is the common table variety. Great chemical industries have located in the
area largely because of the availability of salt, which they use as a raw material, and
the Detroit River. The major firms that pump up a solution of water and salt are Wyandotte
Chemicals Corporation, Pennsylvania Salt Manufacturing Company, and Solvay Process
Division of allied Chemical and Dye Corporation.
Several hundred chemical and pharmaceutical products are made
from the brines and have many commercial uses. When we see a motion picture or ride in a
car with a purring motor we seldom remember that it may be bromine from the Marshall brine
that was used for the silver bromide that makes the film possible. When we ride over a
dustless country road we do not remember that it may be calcium chloride from the Marshall
brines that settles the dust. And it is almost beyond imagination to realize that the
light truck that passes us or the airplane flying overhead was made from metallic
magnesium taken from these brines and that some of the magnesium salts went into the
making of milk of magnesia. True, Michigans other brines are also a source of
chemicals from which hundreds of products are made and are byproducts of the salt and of
the petroleum industry, but until 1940 the only metallic magnesium produced in the United
States was from those long buried imprisoned sea waters, the Marshall brines under Midland
County. Plants now extract magnesium from sea water and also from the several magnesian
minerals and rocks. Nonetheless, buildings, water supplies, material for medicines and
airplanes, material for dustless roads and knockless motors, chemicals whose proper use as
rock solvents make it possible to drill deeper wells, open up tight rocks and let more oil
escape, materials for the new plastics-all these and many more were stored up for us in a
gray brown sand deposited on a sea floor nearly 310 million years ago.
History of salt brine recovery
However remarkable to products from the Marshall brine seem now, they were after all first
sought and pumped up for the manufacture of ordinary salt. Development of all the other
products came after research in ways to use the waste after the sodium chloride salt was
extracted. So in effect, the brines were the byproduct of a byproduct. And for some
wells, oil was yet another "byproduct" from the salt brine wells. Here's a
recollection of a salt brine well near Grindstone City:
"Angus McCachen said the salt well was drilled over
2000 feet deep. From it they pumped up a black, oily substance, which is thought to have
been oil. So, they filled up the hole for about 50 or 60 ft. and pumped salt. At the
peak of this enterprise the well had a capacity of 125 barrels a day. The brine was pure
salt of excellent quality. The latest improvements were used in this well which was 1030
feet deep. Later, salt was found in other parts of the state, where it could be produced
more cheaply, so salt making was discontinued here (at Grindstone City)."
The story of the salt industry in Michigan after 1859 begins in
the Saginaw Valley, which at the time was the scene of great lumbering activities. Saw
mills buzzed and hummed, piling up great heaps of refuse as the logs became lumber---bark,
sawdust, and wood slabs. So the East Saginaw Manufacturing Company, having discovered that
brines were in the rock at a depth of 650 feet, decided that salt manufacture could be
made profitable if the fuel were cheap enough. They found the lumbering wastes were
perfectly suited---cheap, and as inexhaustible as the forests. The success of the company
led to a rapid development of the salt industry throughout the Saginaw valley and spread
to all the lumbering towns along the shores of Lake Huron and Saginaw Bay--from Oscoda and
East Tawas to Harbor Beach; later it spread inland to St. Louis and Midland. Eventually
salt manufacture became a byproduct of the lumbering industry at Manistee and Ludington
also, but a deeper brine in older rocks (Detroit River formation: Devonian) was used. When
the lumber was gone, and the lumber towns vanished, the salt industry vanished with them,
but only in the vanished towns. The byproduct industry then became more important. The
industry continued to develop and to use brines and artificial brines from the Devonian
and Silurian as well as the Mississippian formations. In 16 short years Michigan became
the leading salt producing state--a position held for most of the time since 1876. The
development along the St. Clair and Detroit rivers was independent of the lumber
industry--as the entire industry is today. The salt industry is just one example of the
close relationship of the uses of our natural resources. We were not compelled to cut all
the forests to make salt--but because use of refuse did develop another industry we have
few unsightly piles of decaying sawdust and lumber mill refuse. Let your imagination soar
a bit from a white pine seed to forest-lumbering-refuse-salt
brines-salt-bitterns-magnesium-airplane?
Salt Brines in St. Clair County
St. Clair County, in the thumb region of Michigan, lies on a sheet of salt. In downtown
St. Clair, salt has been mined by brine mining since 1886 when Diamond Crystal Salt opened
up. The factory itself covers approximately 600,000 square feet. Akzo Salt Company bought
it out around 1990 and the current owners, Cargill Salt, bought Akzo out.
In the process of brine mining, fresh water from Cargill is pumped up to the Consumers
Energy Plant in Marysville. At the plant, a drilling rig comes in and drills down about 50
feet and then they drive a 10-inch wide, 50 foot long pipe into the ground. Using water,
they soften the clay so they can continue drilling. After another 50 feet they drive
another length of pipe into the ground, and so on, until they reach the salt bed. They
cement around the 10-inch pipe, the end of which is now approximately 250 feet under the
surface. Inside of the 10-inch pipe, they set a 7-inch pipe, also known as a stringer. The
7-inch pipe goes to the bottom and they then install the wellhead. Next the shutdown valve
and the manual block valve are installed. Now the live pipes are connected to and from the
cavern and tied into the freshwater from Cargill to Consumers Energy and from Consumers
Energy to Cargill. Fresh water is pumped from Cargill to Consumers Energy down the 7-inch
pipe into the cavern at a flow rate of about 75 to 240 GPM. If the water entry is slow, it
dissolves the harder salt faster. To protect the roof of the cavern, so it does not
collapse, propane is injected into the one side of the 10-inch line. It is lighter than
water and can protect the roof from being dissolved as well. After enough salt it
dissolved, it is pumped out the other side of the 10-inch pipe and into a brine pond where
about 95% is sent back to Cargill to undergo the cleaning and evaporation process. In
order for the water to evaporate, temperatures of the brine must reach about 280 degrees
Fahrenheit.
Chemicals (other than NaCl) from salt brine
In 1890, a young chemist named Herbert Henry Dow developed a process
for extracting chemicals from brine. He reactivated an old brine well in Midland, where
the first successful salt well had been put down in the 1870s, and showed that his process
worked. Several years later, he organized the Dow Chemical Company to make bleach
from the extracted chlorine. A profusion of other products followed, and today Midland is
the site of Dows massive chemical complex. Dow also produces bromine and magnesium
compounds at Ludington, where the search for salt began in 1883.
Parts of this page were contributed by GEO 333 student Kara McWain.
This material has been compiled for educational use only,
and may not be reproduced without permission. One copy may be printed for
personal use. Please contact Randall Schaetzl (soils@msu.edu)
for more information or permissions. |