OTHER FOREST PRODUCTS
Back in 1935 and 1940, forest economists, armed with the first complete inventory of the
UP forests, predicted an almost total decline of forest industries in this area. It just
didnt happen! Small sawmills replaced the old, obsolete large mills, and pulpwood demand shifted in emphasis from spruce and fir to aspen,
which had previously been considered to be a worthless "weed tree".
Besides the jobs and wages produced getting forest products to the
industries that needed them, at manufacturing plants such as sawmills, veneer mills, box
plants, flooring mills, cedar fence plants, pulp and paper mills, and others not including
furniture industries, the value added to forest products through manufacture amounted to
millions of dollars per year. This represents many more people employed in these
industries, and the "value added" is more wages, services, taxes, equipment, and
utilities, all of which is additional income. Such items as storage, handling,
advertising, sales costs, and transportation of finished products are more difficult to
assess, but do generate considerable volumes of income to add to this total.
Few people realize the varied nature and numbers of industries
dependent on the forests for raw materials. Much more important, of course, are the many
workers employed and the income they receive.
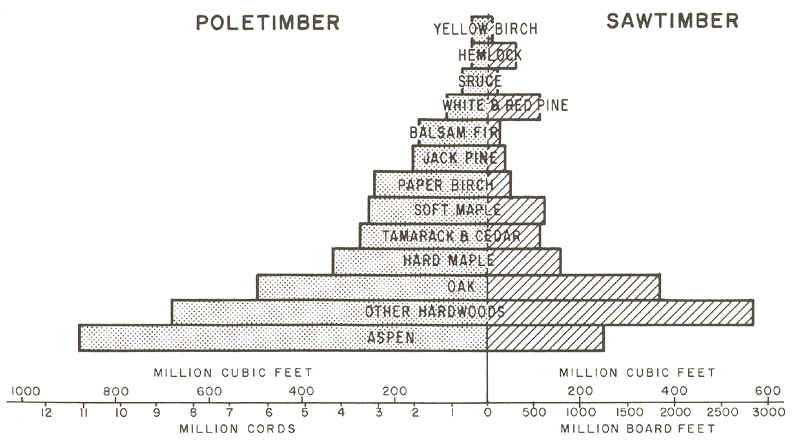
Source: Unknown
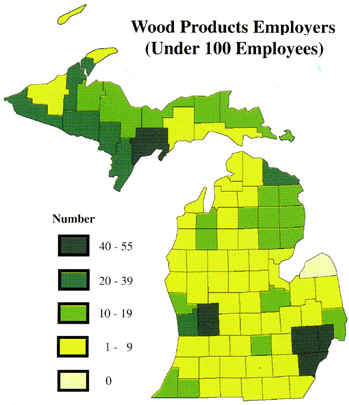 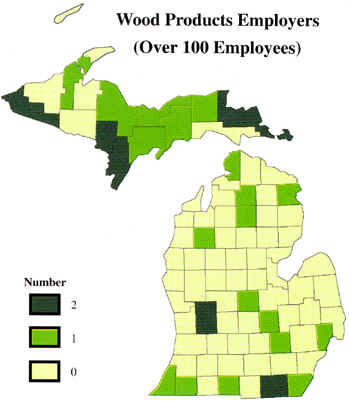
The "placemat" maps (above) were produced by the Michigan
Geographic Alliance and the Science/Mathematics/Technology Center, Central Michigan
University, with funding from the U.S. Dept. of Education. For further information email Wayne.E.Kiefer@cmich.edu
Maple Syrup
Michigan ranks sixth in the nation in maple syrup production (there are ten major
producing states), with an estimated 88,000 gallons of production in 1996 and 73,000
gallons of maple syrup in 1999. Average price received per gallon (in 1993) was
$27.20, compared to $25.50 in 1992.
Vermont is America's leading producer. The collection of sap begins in early spring each
year, when the days begin to warm
but temperatures still dip below freezing at night. The trees must be at least 10 inches
in diameter to be tapped, and as the tree grows, more taps are added.
It takes approximately 40 gallons of sap to produce one gallon of
syrup. The excess water is boiled off in order to concentrate the sugars. A container of
maple syrup can be stored on the shelf until it is ready to be used, but once it is
opened, it should be stored in the refrigerator.
Due to the great increases in charcoal use for picnics, camping, and
home barbecues, the volumes of wood used for this product has increased appreciably during
recent years. Michigan is one of the nations largest charcoal producing states. We
also produce an important amount of chips, slabwood, and veneer cores which would
otherwise be wasted by other wood using industries. As a benefit to the forests, these
industries are extremely important, being a market for the unsound, crooked, or
poor-quality trees which need to be removed, but are wanted by no one else. Elimination of
such material from the forests is one of the basic steps in good management.
These are the most important primary wood-using industries, but there
are many more, such as utility poles, piling, railroad ties, mining timbers, excelsior
wood (to Wisconsin), and large quantities of fuelwood, all of which create jobs, require
equipment, and product wages and saleable products. They all use wood cut from the
forests.
Cedar products
In many parts of Michigan vast acreages of cedar swamps exist. These swamps provide
raw materials such as cedar logs (for "log cabins", fence posts (cedar fence
posts decay very slowly, and thus are very much in demand), and cedar bark for landscaping
and mulch. Because cedar swamps are wet places, much of the logging must be done in
winter, when the soils are frozen and beneath a snowpack.
Veneer
Wood veneer extremely thin sheet of rich-coloured wood (such as mahogany, ebony, oak, or
rosewood) cut in thin sheets and applied to the surface area of a piece of lower quality
wood. There are two main types of veneering, the simplest being that in which a
single sheet, chosen for its interesting grain (yew or purple wood, for example), is
applied to a whole surface of inferior wood in one unit. In the more complex variation
called crossbanding, small pieces of veneer wood are fitted together within a surrounding
framework in such a way that the grain changes pattern, thus altering the tone according
to the light. This process can produce complex fan shapes, sunbursts, and floral patterns.
When the veneers are made up of small pieces cut from the same larger piece of wood and
affixed so that their grain runs in opposite directions in accordance with a formal
geometric
pattern, the process is known as parquetry.
Veneering allows the use of beautiful woods that because of limited availability, small
size, or difficulty in working cannot be used in solid form for making furniture. In
addition, it significantly increases the strength of the wood by backing it with a
sturdier wood and, through the process of laminating veneers at right angles in successive
layers, offsets the cross-grain weakness of the wood. Michigan is a large producer
of veneer woods, especially oak and birdseye maple.
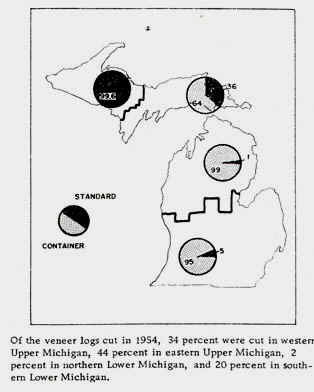
Source: Unknown
Secondary Forest Products
Sawlogs, pulpwood, and firewood is cut in forests, and in so doing creates many
jobs in the primary wood-using industry. Next comes the secondary industries
which use the lumber, the pulp, or the paper for further manufacture into products for the
ultimate consumer. There are flooring mills, crate mills, box and pallet plants, furniture
and fixture plants, and many more, including a few paper and paper products plants.
In this secondary phase, the wood-using industries employ at least
twice as many people as have been employed up to this point, and pay wages, taxes,
utilities, services, and add the largest part to the total income which comes to Michigan
from its forests. There are so many items of equipment and wages involved along the way,
and so much manufacturing, that neither time nor space permit a full accounting. Suffice
it to say that there are chain-saws (gas and oil for them, too), axes, wedges, chains,
tractors, trucks, cranes, hoists, steel cable, gloves, clothing, groceries, autos to carry
people to and from work, homes, haircuts, fishing tackle, beer, guns, newspapers, iodine,
and bandages, all paid for by this work.
These people help support the schools, roads, and local government.
And, speaking of roads, it should be pointed out that on an average, one mile of woods
road must be constructed for hauling each 1,200 cords of pulpwood cut, or 600 thousand
board feet of logs. This results in the construction of many miles of roads usable by
hunters, berry-pickers, fishermen, and campers, none of whom could have brought in the
needed gravel fill, built the small bridges, or installed the necessary culverts! These
forest visitors in pursuit of recreation also spend large volumes of money in the areas
which they frequent.
Fortunately, these "working forests" from which such wealth
of income is derived also produce more animals and birds, provide continuous changes in
the scenery, favor the production of many flowers and berries, and do an excellent job of
water conservation, maintaining relatively stable flow and even temperatures in the trout
streams. Without use of the products, these benefits would be lessened, and without the
work and wages, many less people would be able to enjoy them.
Here's an interesting story about one gentleman who bought some wooded land in Michigan
and got "more than he'd bargained for".
The asking price for the woodlot at that time, about 1963, was $1,700.
My advisor/friend, Charlie Peterson told me to buy it, so I did. Soon after I sold just
the elm trees on the woodlot to the Michigan Maple Block Company in Petoskey who make
hardwood butcher blocks of all kinds. They looked it over and paid me $1,700 for the elm.
Dutch elm disease was just starting, so this was a good move. A few years later I sold the
maple and basswood trees for $8,000. So you see, in many ways, money does grow on
trees. After this, we had other timber sales from the woodlot, usually with the aid of a
registered forester.
Then we clear-cut the aspen (formerly thought of as a weed tree and now
the most important ingredient in particle board), which went into chips for plywood.
Chipping eats up everything from the trunk to the tip, including branches, needles and
all, leaving the forest floor clean. This operation lasted two years and consisted of
whole trees being cut, skidded and run through a chipper on the site, then hauled by big
trucks to the mill.
Our latest timber harvest consisted of a red pine thinning of trees
planted 40 years ago, with every third row being taken out and cut in eight-foot lengths.
These were transported by semi-truck to the Weyerhaeuser structurewood plant in Grayling.
The remaining trees, now getting the benefit of sunlight and room, will expand and grow
more rapidly. The next cut, Im told, will be in large poles which have more value
than sawlogs.
Parts of the text above have been paraphrased from C.M.
Davis Readings in the Geography of Michigan (1964).
This material has been compiled for educational use only, and
may not be reproduced without permission. One copy may be printed for personal
use. Please contact Randall Schaetzl (soils@msu.edu)
for more information or permissions.
|